Written by Ian Scheffler
September 25, 2024
One of the greatest challenges in the fight against climate change is energy storage. Fossil fuel essentially stores itself, with its energy locked inside its own chemical bonds. But how do you store more sustainable, but otherwise ephemeral, forms of energy, like the power of the wind and sun?
For Eric Detsi, Associate Professor in Materials Science and Engineering (MSE), the answer is batteries, with the caveat that batteries powerful enough to meet the future’s energy demands — the International Energy Agency projects that worldwide battery capacity will need to sextuple by 2030 — do not yet exist.
In most batteries used today, from the disposable alkaline batteries in household appliances like alarm clocks to the rechargeable lithium-ion batteries in hybrid and electric vehicles, the electrodes between which ions flow are typically made of solid materials like metal oxides or graphite. But, as Detsi points out, each cycle of charging and discharging the battery damages the material, because the electrodes expand and contract, sometimes by as much as 300%, which is one of the reasons why even rechargeable batteries gradually lose capacity and eventually fail.
“There is a need for materials that can store a large amount of lithium, sodium and magnesium for use in high-performance batteries,” says Detsi. “The problem is that the more lithium, sodium or magnesium a battery material can store, the more it expands and shrinks during charging and discharging, resulting in huge volume change.”
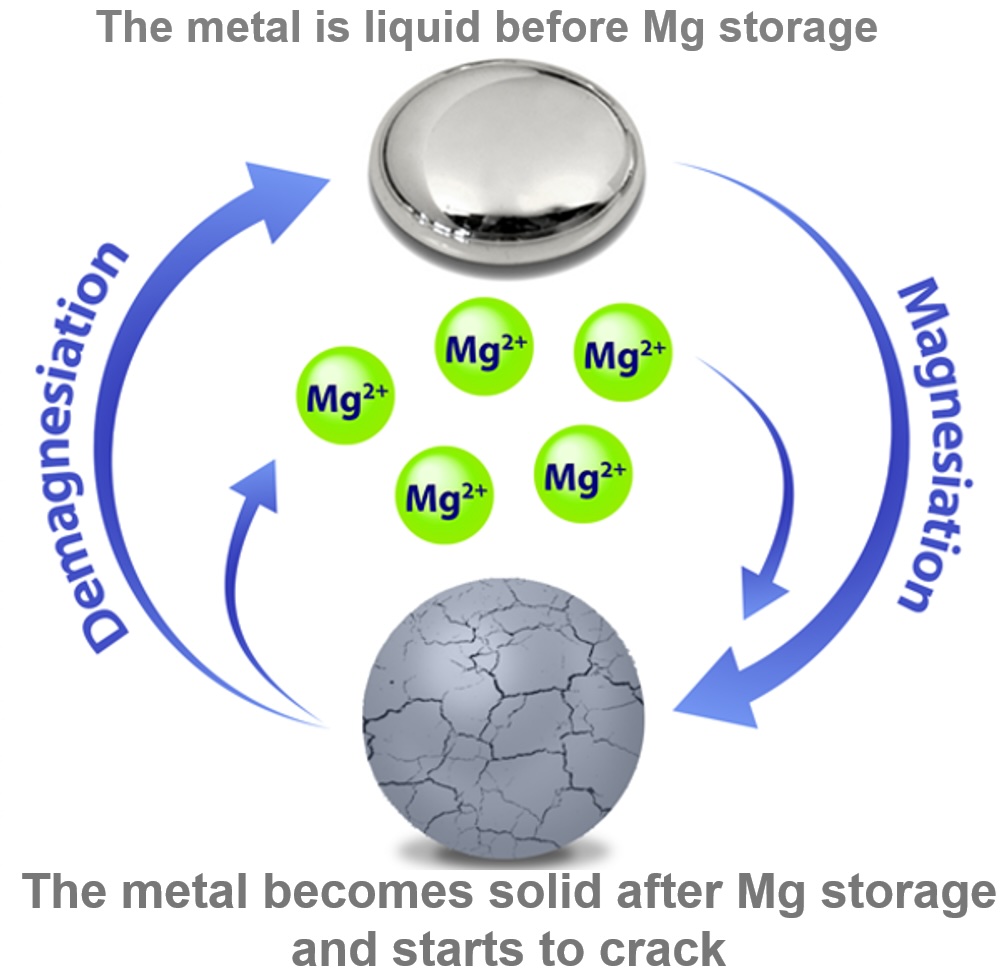
Some researchers, including the late 2019 Nobel laureate John Goodenough, one of the fathers of lithium-ion batteries, recently started to develop batteries with liquid electrodes, which don’t break when their volume changes. But liquid electrodes present other challenges, namely the difficulty of safely manufacturing and using batteries that behave like water balloons. In other words, just building larger or liquid batteries won’t work — to design the batteries of the future, researchers will need to create entirely new materials.
What’s more, many of the elements typically used in mass-produced, rechargeable batteries — like lithium and cobalt — are becoming increasingly expensive, not to mention entangled in human rights abuses, as demand for batteries increases. (Last year, Siddarth Kara, a professor at the University of Nottingham, published Cobalt Red: How the Blood of the Congo Powers Our Lives, an exposé about the abysmal labor practices in the Democratic Republic of the Congo, which produces three-quarters of the world’s cobalt.) “The need for high-performance batteries for emerging energy storage applications such as grid-scale storage and electric vehicles led me to study materials for batteries,” says Detsi.
To that end, his group has been studying batteries made primarily of sodium and magnesium, which are cheaper and less ethically fraught since sodium and magnesium are plentiful in the earth’s crust. More importantly, sodium and magnesium resources are abundant in the U.S. For example, according to the U.S. Geological Survey (USGS), 68.8% of the world’s reserves of sodium carbonate (soda ash) and 14.5% of the world’s sodium chloride (salt), which are needed to make sodium, are found in the U.S.
Detsi’s group is using these metals to develop electrodes that shift between liquid and solid states to avoid damage during charge cycles while still being easy to manufacture. “When the material is in the solid phase, it will start degrading due to the huge volume changes occurring during charge storage,” says Detsi. “However, when the material transforms from solid to liquid, it ‘heals’ itself by recovering from volume-change-induced degradation.”
At first, Detsi demonstrated the feasibility of this approach using an anode — the electrode that collects ions during charging — made of dimagnesium pentagallide (Mg2Ga5), a mixture of magnesium and gallium, the latter of which has a low melting point, making it easy for such alloys to shift from solid to liquid.
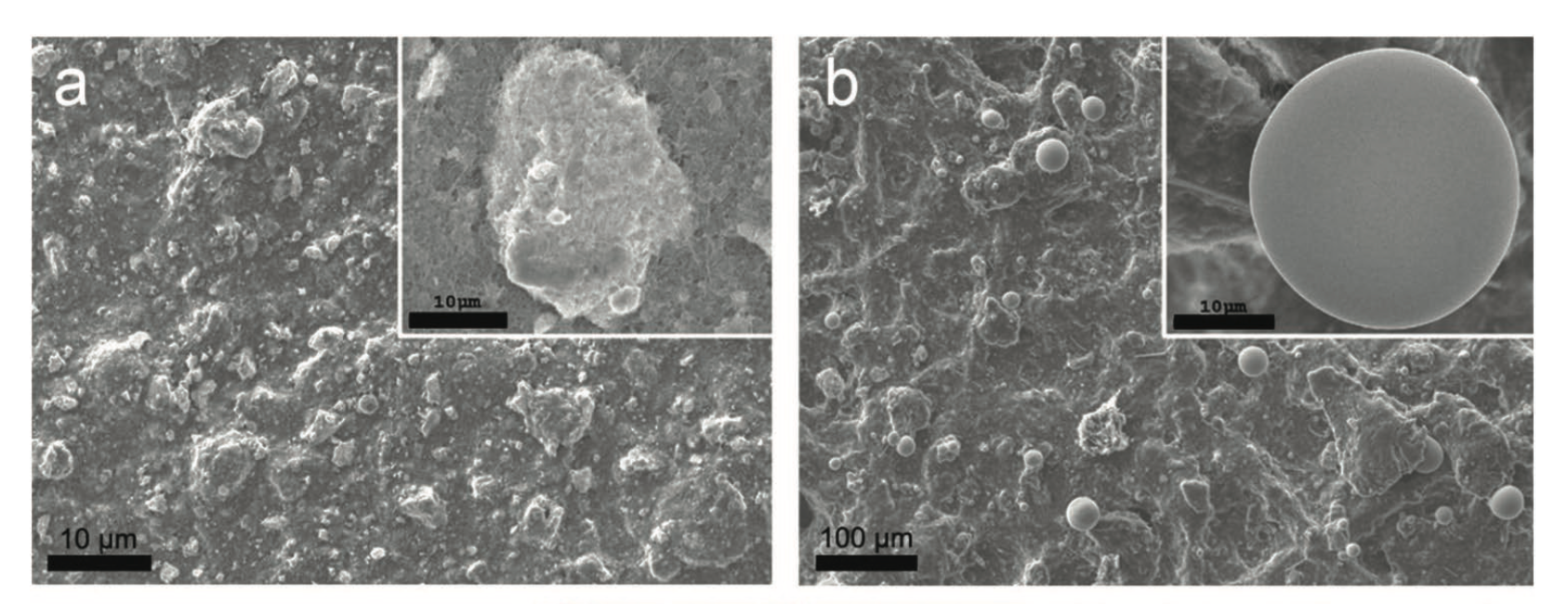
In 2019, Detsi’s lab, along with that of Vivek Shenoy, Eduardo D. Glandt President’s Distinguished Professor in MSE, in Mechanical Engineering and Applied Mechanics (MEAM), and in Bioengineering (BE), showed that self-healing anodes made of Mg2Ga5 could withstand more than 1000 charge cycles. “Before our work,” says Detsi, “the cycle life of state-of-the-art magnesium-ion battery anodes was only 200 cycles.” In other words, the addition of the self-healing anode quintupled the initial lifespan of magnesium-ion batteries.
Earlier this year, Detsi’s lab pushed the envelope even further, using a gallium-indium anode that melts at room temperature, potentially opening the door to commercial applications. The experimental anode survived 2,000 charging cycles while retaining 91% battery capacity. “This is unprecedented,” says Detsi. For context, the iPhone 15 can sustain 1000 charging cycles while retaining 80% battery capacity.
In order to advance the project, Detsi and his coauthors — Lin Wang and Alexander Ng, recent Ph.D. graduates, and Roxana Family, a postdoctoral fellow — employed a variety of advanced imaging techniques to better understand the material’s transformation from solid to liquid, including X-ray diffraction, X-ray scattering, X-ray spectroscopy and cryogenic scanning electron microscopy. The latter technique involves freezing the liquid metal anodes at different stages, to better study the self-healing process, as Detsi and his group described in a 2023 paper published by the American Chemical Society.
Nearly a decade ago, when Detsi and his group started exploring the concept of self-healing sodium- and magnesium-ion batteries, hardly anyone took his ideas seriously. “I remember a reviewer of one of our proposals on sodium-ion batteries asking why sodium-ion batteries are not commercialized if they are so great,” Detsi says. “At the time, there was only one startup company developing sodium-ion batteries. Now there are many across the globe.”
These studies were conducted at the University of Pennsylvania School of Engineering and Applied Science and supported by the U.S. National Science Foundation (NSF) Civil Mechanical and Manufacturing Innovation (CMMI) EArly-concept Grant for Exploratory Research (EAGER) award #1840672, NSF Division of Materials Research (DMR) Future Manufacturing award #2134715, and NSF-CMMI Faculty Early Career Development Program (CAREER) award #2047851.
Other co-authors of these studies include Jintao Fu, Mohammed H. Hassan, Hyeongjun Koh, Hemant Kumar, Stella Lin, Eric Stach and Samuel S. Welborn of Penn Engineering; Manni Li and Zeyu Wang of the Harbin Institute of Technology; Harsh Dilipkumar Jagad and Yue Qi of Brown University; and William R. Fullerton and Christopher Y. Li of Drexel.